Hard anodising
Hard anodising is a variation of normal anodising. It is a process in which the aluminium is provided with a very hard wear-resistant layer several times thicker than in standard anodising.
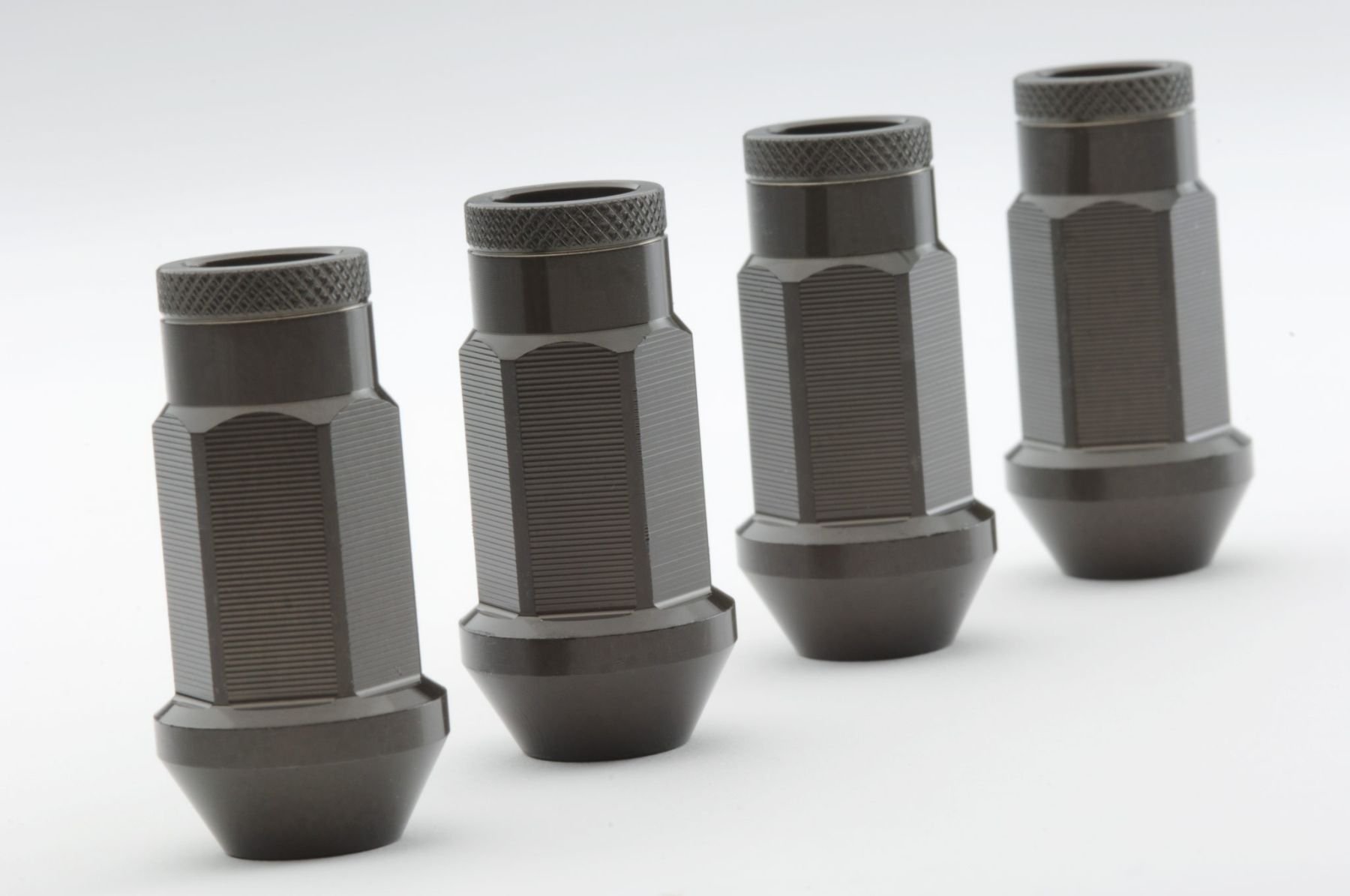
We help find the right surface treatment
Get in touchThrough hard anodising, layer thicknesses of up to 150 microns (0.15 millimetres) can be achieved. The layer is highly scratch- and wear-resistant and has extremely high corrosion resistance and hardness. Post-processing such as grinding and honing of the anodic layer is common since hard anodising increases the roughness of the starting product.
The process takes place in a bath filled with an electrolyte that is strongly cooled. Hard anodising requires higher current densities compared to normal anodising. This therefore creates smaller pores than normal.
A hard anodised layer is by definition darker than a normal anodised layer because of its greater thickness. The colour ranges from anthracite to black. Because of the smaller pores, colouring a hard anodic layer is difficult but not impossible. Also, the naturally darker colour of the hard anodic layer may be an impediment to achieving the desired colour.
Applications
Aluminium's combination of hardness and lightness is already being gratefully used in the automotive and motorbike industries. For example, hard anodised aluminium shock absorbers can withstand extremely heavy loads, dust, sand and water. Other applications include:
Machine and equipment construction (wear parts, paper rolls)
Aircraft construction (light weight)
Pneumatics (brake cylinders, plungers, pressure rings etc.)
Hydraulics (corrosion protection)
Electronics industry (electrical insulation)
Mechanics (lower inertia)
Offshore industry
Effshore industry