Colour anodising
Aldor BV specialises in colouring anodised aluminium. Meticulous bath control enables excellent colour reproducibility. Coloured anodising layers are possible by impregnative colouring, electrolytic colouring and by self-colouring due to material alloying.
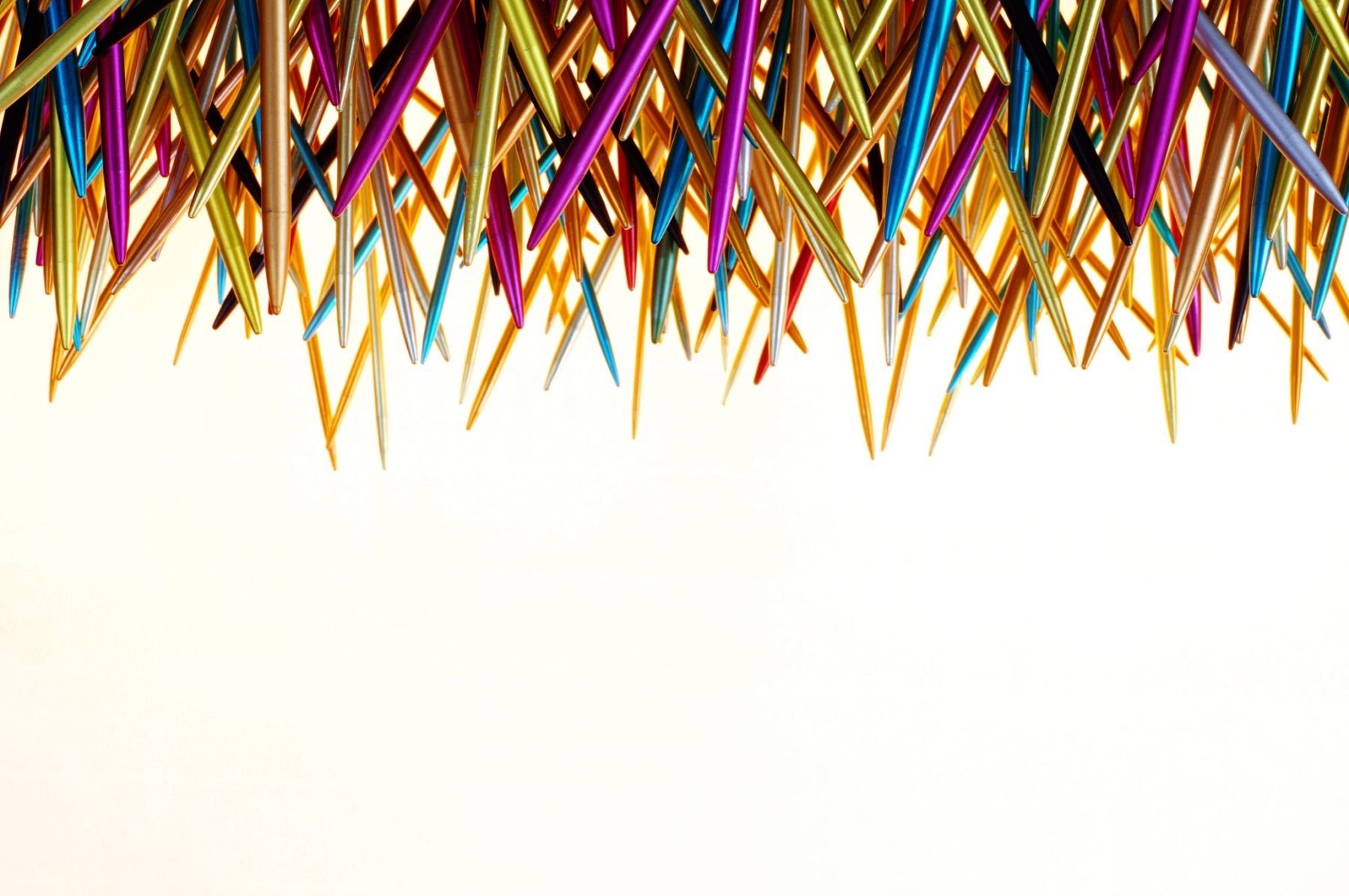
We help find the right surface treatment
Get in touchImpregnation colouring
When colouring anodised aluminium, (an)organic dyes are impregnated into the pores of the anodic layer. Coloured anodic layers offer an unlimited range of colour possibilities with the practical limitation being the presence of appropriate colour baths.

downloads. When colouring organically, the influence of UV light and (strong) acids must be taken into account. These cause the colours to decolourise over time.
Electrolytic colouring
The electrolytic, 2-phase, colouring process at Aldor is PGE Eindhoven's MCDS process and gives a high degree of UV and chemical resistance. Aldor has combined the 2-phase colouring into a 3-phase process that produces deep, optically very nice colours. The workpieces anodised with this 3-phase process are guaranteed to have no bleeding at screw holes and pot holes, as is often the case with impregnative colouring.
The international colour codings commonly used in electrolytic colouring are listed below. The colour examples in the table below are indicative. If you would like to have a colour sample made, this can always be discussed. That way, the final bronze colour can be determined exactly for your product.
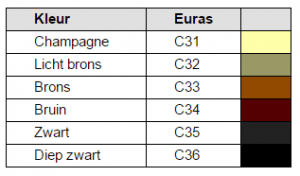
Self-colouring due to alloying
Because the vast majority of aluminium products are made from aluminium alloys, self-colouring due to these alloying components is common. For example, aluminium alloy 7075 colours yellow/gold. This self-colouring is often confused with colour anodising as described above. If you are not sure what the colour of your aluminium alloy will be after anodising, please contact Aldor in good time.